@mimico_polak the brick deterioration was caused by the insulation on the inside (brick now gets wet and does not dry out before freezing). Less R and maybe it would not be as bad. Why did he insulate....he was gutting the house for other reasons and decided to go crazy on the grants at the time.
Long ago I was looking at a product from Nadura but sadly was only sold by Rona in QC. It was 4X8 2.5 inch closed cell foam boards that fit together with built in strapping. Just slap it up, secure it, install some outlets, drywall on-top, and go for a beer. No framing required.
****
On the brick, not just inusaltion is a problem, we actually have some deterioration from the neighbours hot water heater with an exhaust between the houses. Blasts our brick with hot moist air all winter long. CSA no longer allows exhausts in this situation for this reason in new installs (must be min 3 feet from property line now assuming I remember this code properly--but I still see gas guys doing it), we are four feet between the houses. I plan on doing some hardie or cedar in a decorative way to protect our brick here.
Long ago I was looking at a product from Nadura but sadly was only sold by Rona in QC. It was 4X8 2.5 inch closed cell foam boards that fit together with built in strapping. Just slap it up, secure it, install some outlets, drywall on-top, and go for a beer. No framing required.
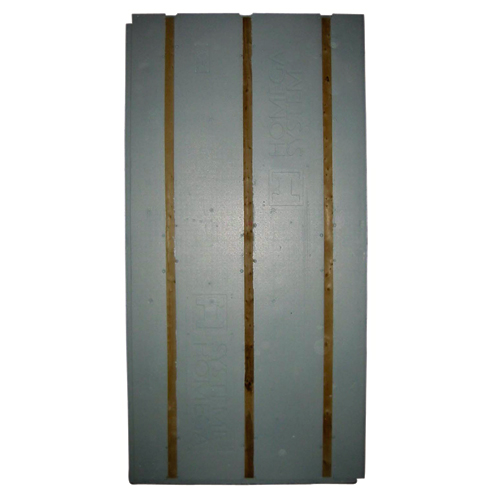
****
On the brick, not just inusaltion is a problem, we actually have some deterioration from the neighbours hot water heater with an exhaust between the houses. Blasts our brick with hot moist air all winter long. CSA no longer allows exhausts in this situation for this reason in new installs (must be min 3 feet from property line now assuming I remember this code properly--but I still see gas guys doing it), we are four feet between the houses. I plan on doing some hardie or cedar in a decorative way to protect our brick here.